Chemische injectieleidingen onder in het boorgat - Waarom falen ze?Ervaringen, uitdagingen en toepassing van nieuwe testmethoden
Copyright 2012, Vereniging van Petroleum Engineers
Abstract
Statoil exploiteert verschillende velden waar continue injectie van aanslagremmer in het boorgat wordt toegepast.Het doel is om de bovenste slang en veiligheidsklep te beschermen tegen (Ba/Sr) SO4orCaCO;schaal, in gevallen waarin het regelmatig moeilijk en kostbaar is om de schaal samen te persen, bijv. koppeling van onderzeese velden.
Continue injectie van aanslagremmer in het boorgat is een technisch geschikte oplossing om de bovenste slangen en veiligheidsklep te beschermen in putten die aanslagpotentieel hebben boven de productiepakker;vooral in putten die niet regelmatig hoeven te worden afgetapt vanwege het potentieel voor schaalvergroting in het nabije boorgatgebied.
Het ontwerpen, bedienen en onderhouden van de chemicaliëninjectielijnen vraagt om extra aandacht voor materiaalkeuze, chemicaliënkwalificatie en monitoring.Druk, temperatuur, stroomregimes en geometrie van het systeem kunnen een uitdaging vormen voor een veilige werking.Uitdagingen zijn geïdentificeerd in de kilometerslange injectieleidingen van de productiefaciliteit naar de onderzeese mal en in de injectiekleppen beneden in de putten.
Praktijkervaringen die de complexiteit van continue injectiesystemen onder in het boorgat aantonen met betrekking tot problemen met neerslag en corrosie worden besproken.Laboratoriumstudies en toepassing van nieuwe methoden voor chemische kwalificatie zijn vertegenwoordigd.Er wordt ingegaan op de behoefte aan multidisciplinaire acties.
Invoering
Statoil exploiteert verschillende velden waar continue injectie van chemicaliën in het boorgat is toegepast.Dit omvat voornamelijk injectie van aanslagremmer (SI) waarbij het doel is om de bovenste buis en de veiligheidsklep (DHSV) in het boorgat te beschermen tegen (Ba/Sr) SO4orCaCO;schaal.In sommige gevallen wordt emulsiebreker in het boorgat geïnjecteerd om het scheidingsproces zo diep mogelijk in de put te starten bij een relatief hoge temperatuur.
Continue injectie van ketelsteenremmer in het boorgat is een technisch geschikte oplossing om het bovenste deel van de putten die aanslagpotentieel hebben boven de productiepakker te beschermen.Continue injectie kan worden aanbevolen, met name in putten die niet hoeven te worden samengeperst vanwege het lage scaling-potentieel in de nabije boorput;of in gevallen waar schaalafpersing moeilijk en kostbaar kan zijn om regelmatig uit te voeren, bijv. koppeling van onderzeese velden.
Statoil heeft uitgebreide ervaring op het gebied van continue injectie van chemicaliën in systemen aan de bovenzijde en onderzeese sjablonen, maar de nieuwe uitdaging is om het injectiepunt dieper in de put te brengen.Het ontwerpen, bedienen en onderhouden van de chemie-injectielijnen vraagt om extra aandacht op meerdere onderwerpen;zoals materiaalkeuze, chemische kwalificatie en monitoring.Druk, temperatuur, stroomregimes en geometrie van het systeem kunnen een uitdaging vormen voor een veilige werking.Uitdagingen in lange (meerdere kilometers) injectieleidingen van de productiefaciliteit naar de onderzeese sjabloon en naar de injectiekleppen beneden in de putten zijn geïdentificeerd;Figuur 1.Sommige injectiesystemen hebben volgens plan gewerkt, andere zijn om verschillende redenen uitgevallen.Er zijn verschillende nieuwe veldontwikkelingen gepland voor chemische injectie in het boorgat (DHCI);Echter;in sommige gevallen is de apparatuur nog niet volledig gekwalificeerd.
Toepassing van DHCI is een complexe taak.Het gaat om de afronding en putontwerpen, putchemie, deksysteem en het chemicaliëndoseersysteem van het dekproces.De chemicaliën worden van bovenaf via de chemicaliëninjectieleiding naar de afwerkingsapparatuur en in de put gepompt.Bij de planning en uitvoering van dit soort projecten is samenwerking tussen verschillende disciplines dan ook cruciaal.Verschillende overwegingen moeten worden afgewogen en een goede communicatie tijdens het ontwerp is belangrijk.Er zijn procesingenieurs, subsea-ingenieurs en voltooiingsingenieurs bij betrokken, die zich bezighouden met de onderwerpen putchemie, materiaalkeuze, stromingszekerheid en beheer van productiechemicaliën.De uitdagingen kunnen chemische pistoolkoning of temperatuurstabiliteit, corrosie en in sommige gevallen een vacuümeffect zijn als gevolg van lokale druk- en stromingseffecten in de injectieleiding voor chemicaliën.Daarnaast zijn er omstandigheden zoals hoge druk, hoge temperatuur, hoge gassnelheid, hoog aanslagpotentieel,navelstreng over lange afstand en diep injectiepunt in de put, geven verschillende technische uitdagingen en eisen aan de geïnjecteerde chemicaliën en aan de injectieklep.
Een overzicht van de DHCI-systemen die bij Statoil-operaties zijn geïnstalleerd, laat zien dat de ervaring niet altijd succesvol is geweest. Tabel 1. Er wordt echter gewerkt aan plannen voor verbetering van het injectieontwerp, de chemische kwalificatie, de bediening en het onderhoud.De uitdagingen variëren van veld tot veld en het probleem is niet noodzakelijkerwijs dat de chemische injectieklep zelf niet werkt.
In de afgelopen jaren zijn er verschillende uitdagingen geweest met betrekking tot ondergrondse chemische injectielijnen.In dit artikel worden enkele voorbeelden gegeven van deze ervaringen.De paper bespreekt uitdagingen en maatregelen die zijn genomen om de problemen met betrekking tot DHCI-lijnen op te lossen.Er worden twee casuïstiek gegeven;een over corrosie en een over de koning van chemische wapens.Praktijkervaringen die de complexiteit van continue injectiesystemen onder in het boorgat aantonen met betrekking tot problemen met neerslag en corrosie worden besproken.
Laboratoriumstudies en toepassing van nieuwe methoden voor chemische kwalificatie worden ook overwogen;hoe de chemische stof moet worden gepompt, aanslagpotentieel en preventie, complexe apparatuurtoepassing en hoe de chemische stof het systeem aan de bovenzijde zal beïnvloeden wanneer de chemische stof terug wordt geproduceerd.Aanvaard criteria voor chemische toepassing hebben betrekking op milieukwesties, efficiëntie, opslagcapaciteit bovenzijde, pompsnelheid, of bestaande pomp kan worden gebruikt enz. Technische aanbevelingen moeten gebaseerd zijn op vloeistof- en chemiecompatibiliteit, restdetectie, materiaalcompatibiliteit, onderzeese navelstrengontwerp, chemisch doseringssysteem en materialen in de omgeving van deze lijnen.De chemische stof moet mogelijk worden gehydrateerd om verstopping van de injectieleiding door binnendringen van gas te voorkomen en de chemische stof mag niet bevriezen tijdens transport en opslag.In de bestaande interne richtlijnen is een checklist opgenomen van welke chemicaliën op elk punt in het systeem kunnen worden toegepast. Fysische eigenschappen zoals viscositeit zijn belangrijk.Het injectiesysteem kan een afstand van 3-50 km van de navelstreng onderzeese stroomlijn en 1-3 km naar beneden in de put impliceren.Daarom is de temperatuurstabiliteit ook belangrijk.Evaluatie van stroomafwaartse effecten, bv. in raffinaderijen, kan ook overwogen moeten worden.
Downhole chemische injectiesystemen
Kostenvoordeel
Continue injectie van ketelsteenremmer in het boorgat om de DHS te beschermen tegen de productieslang kan kosteneffectief zijn in vergelijking met het persen van de put met ketelsteenremmer.Deze toepassing vermindert de kans op schade aan de formatie in vergelijking met behandelingen voor het samendrukken van kalkaanslag, vermindert de kans op procesproblemen nadat een kalkaanslag is samengedrukt en biedt de mogelijkheid om de injectiesnelheid van chemicaliën te regelen vanaf het injectiesysteem aan de bovenzijde.Het injectiesysteem kan ook worden gebruikt om andere chemicaliën continu in het boorgat te injecteren en kan daardoor andere uitdagingen verminderen die zich verder stroomafwaarts van de procesinstallatie kunnen voordoen.
Er is een alomvattende studie uitgevoerd waarbij een strategie op boorgatschaal voor het Oseberg S of -veld werd ontwikkeld.De grootste zorg was CaCO;schilfering in de bovenste slang en mogelijke DHSV-storing.Uit de overwegingen van de Oseberg S of schaalbeheerstrategie bleek dat DHCI over een periode van drie jaar de meest kostenefficiënte oplossing was in de putten waar de chemicaliëninjectielijnen functioneerden.Het belangrijkste kostenelement met betrekking tot de concurrerende techniek van scale squeeze was de uitgestelde olie in plaats van de chemische/operationele kosten.Voor de toepassing van aanslagremmer in gaslift was de belangrijkste factor voor de chemische kosten de hoge gasliftsnelheid die leidde tot een hoge SI-concentratie, aangezien de concentratie in evenwicht moest worden gehouden met de gasliftsnelheid om chemische pistoolkoning te voorkomen.Voor de twee putten op Oseberg S of die goed functionerende DHC I-lijnen hadden, werd voor deze optie gekozen om de DHS V's te beschermen tegen CaCO;schaalvergroting
Continu injectiesysteem en kleppen
Bestaande voltooiingsoplossingen die gebruik maken van continue chemische injectiesystemen staan voor uitdagingen om verstopping van de capillaire leidingen te voorkomen.Het injectiesysteem bestaat typisch uit een capillaire leiding, 1/4" of 3/8" buitendiameter (OD), aangesloten op een verdeelstuk aan het oppervlak, doorgevoerd en verbonden met de slanghanger aan de ringvormige zijde van de slang.De capillaire leiding is bevestigd aan de buitendiameter van de productieslang door middel van speciale slangkraagklemmen en loopt aan de buitenkant van de slang helemaal naar beneden tot aan de doorn voor de injectie van chemicaliën.De doorn wordt traditioneel stroomopwaarts van de DHS V of dieper in de put geplaatst met de bedoeling de geïnjecteerde chemische stof voldoende tijd te geven om te verspreiden en de chemische stof daar te plaatsen waar de uitdagingen worden gevonden.
Bij de chemische injectieklep, figuur 2, bevat een kleine patroon met een diameter van ongeveer 4,5 cm de terugslagkleppen die voorkomen dat boorvloeistoffen de capillaire leiding binnendringen.Het is gewoon een kleine schotel die op een veer rijdt.De veerkracht bepaalt en voorspelt de druk die nodig is om de schotel van de afdichtzitting te openen.Wanneer de chemische stof begint te stromen, wordt de schotel van zijn zitting getild en opent de terugslagklep.
Het is verplicht om twee keerkleppen te installeren.Eén klep is de primaire barrière die verhindert dat boorvloeistoffen de capillaire leiding binnendringen.Deze heeft een relatief lage openingsdruk (2-15 bar). Als de hydrostatische druk in de capillaire leiding lager is dan de boorputdruk, zullen de boorvloeistoffen proberen de capillaire leiding binnen te dringen.De andere terugslagklep heeft een atypische openingsdruk van 130-250 bar en staat bekend als het U-tube preventiesysteem.Deze klep voorkomt dat de chemische stof in de capillaire leiding vrijelijk in de boorput stroomt als de hydrostatische druk in de capillaire leiding groter is dan de druk in de boorput op het injectiepunt van de chemische stof in de productiebuis.
Naast de twee terugslagkleppen is er normaal gesproken een in-line filter, het doel hiervan is om ervoor te zorgen dat geen enkel soort vuil de afdichtingsmogelijkheden van de terugslagklepsystemen in gevaar kan brengen.
De afmetingen van de beschreven terugslagkleppen zijn vrij klein en reinheid van de geïnjecteerde vloeistof is essentieel voor hun operationele functionaliteit.Aangenomen wordt dat vuil in het systeem kan worden weggespoeld door de stroomsnelheid in de capillaire lijn te verhogen, zodat de terugslagkleppen opzettelijk openen.
Wanneer de terugslagklep opent, neemt de stromende druk snel af en verspreidt zich omhoog door de capillaire lijn totdat de druk weer toeneemt.De terugslagklep zal dan sluiten totdat de stroom chemicaliën voldoende druk heeft opgebouwd om de klep te openen;het resultaat is drukschommelingen in het terugslagklepsysteem.Hoe hoger de openingsdruk van het terugslagklepsysteem, des te kleiner het doorstroomgebied is wanneer de terugslagklep opent en het systeem probeert evenwichtscondities te bereiken.
De chemicaliëninjectieventielen hebben een relatief lage openingsdruk;en mocht de slangdruk bij het chemicaliëninlaatpunt lager worden dan de som van de hydrostatische druk van chemicaliën in de capillaire lijn plus de openingsdruk van de terugslagklep, dan zal bijna vacuüm of vacuüm optreden in het bovenste deel van de capillaire lijn.Wanneer de injectie van chemicaliën stopt of de stroming van chemicaliën laag is, zullen bijna-vacuümcondities ontstaan in het bovenste gedeelte van de capillaire lijn.
Het vacuümniveau is afhankelijk van de boorputdruk, het soortelijk gewicht van het geïnjecteerde chemische mengsel dat in de capillaire leiding wordt gebruikt, de openingsdruk van de terugslagklep op het injectiepunt en de stroomsnelheid van de chemische stof in de capillaire leiding.De condities van de put zullen gedurende de levensduur van het veld variëren en het potentieel voor vacuüm zal daarom ook in de loop van de tijd variëren.Het is belangrijk om op de hoogte te zijn van deze situatie om de juiste overweging en voorzorgsmaatregelen te nemen voordat verwachte uitdagingen zich voordoen.
Samen met de lage injectiesnelheden verdampen de oplosmiddelen die in dit soort toepassingen worden gebruikt doorgaans, wat effecten veroorzaakt die nog niet volledig zijn onderzocht.Deze effecten zijn pistoolkoning of neerslag van vaste stoffen, bijvoorbeeld polymeren, wanneer het oplosmiddel verdampt.
Verder kunnen galvanische cellen worden gevormd in de overgangsfase tussen het vloeistofoppervlak van de chemische stof en de met damp gevulde nabij-vacuümgasfase erboven.Dit kan leiden tot plaatselijke putcorrosie in de capillaire leiding als gevolg van de toegenomen agressiviteit van de chemische stof onder deze omstandigheden.Vlokken of zoutkristallen die als een film in de capillaire lijn worden gevormd terwijl de binnenkant uitdroogt, kunnen de capillaire lijn blokkeren of verstoppen.
Nou, barrièrefilosofie
Bij het ontwerpen van robuuste putoplossingen vereist Statoil dat de putbeveiliging te allen tijde aanwezig is tijdens de levenscyclus van de put.Statoil vereist dus dat er twee onafhankelijke bronbarrières intact zijn.Fig. 3 toont een atypisch schema van de putbarrière, waarbij de blauwe kleur de omhulling van de primaire putbarrière voorstelt;in dit geval de productieslang.De rode kleur vertegenwoordigt de secundaire barrière-envelop;het omhulsel.Aan de linkerkant in de schets is de chemische injectie aangegeven als een zwarte lijn met een injectiepunt naar de productieslang in het rood gemarkeerde gebied (secundaire barrière).Door chemische injectiesystemen in de put te introduceren, komen zowel de primaire als de secundaire boorputbarrières in gevaar.
Case geschiedenis op corrosie
Volgorde van de gebeurtenissen
Onder in het boorgat is een chemische injectie van aanslagremmer toegepast in een olieveld dat wordt geëxploiteerd door Statoil op het Noorse continentale plat.In dit geval was de aangebrachte aanslagremmer oorspronkelijk gekwalificeerd voor toepassing boven water en onder water.Het opnieuw voltooien van de put werd gevolgd door installatie van DHCIpointat2446mMD, Fig.3.De injectie in het boorgat van de aanslagremmer aan de bovenzijde werd gestart zonder verder testen van de chemische stof.
Na een jaar in bedrijf te zijn geweest, werden lekkages in het chemicaliëninjectiesysteem waargenomen en werd het onderzoek gestart.De lekkage had een nadelig effect op de putbarrières.Soortgelijke gebeurtenissen deden zich voor bij verschillende putten en sommige moesten tijdens het onderzoek worden afgesloten.
De productieslang werd getrokken en tot in detail bestudeerd.De aantasting door corrosie bleef beperkt tot één kant van de buis en sommige buisverbindingen waren zo gecorrodeerd dat er eigenlijk gaten doorheen zaten.Ongeveer 8,5 mm dik 3% chroomstaal was in minder dan 8 maanden uiteengevallen.De belangrijkste corrosie had plaatsgevonden in het bovenste gedeelte van de put, vanaf de putmond tot ongeveer 380 m MD, en de ergste gecorrodeerde buisverbindingen werden gevonden op ongeveer 350 m MD.Beneden deze diepte werd weinig of geen corrosie waargenomen, maar er werd veel puin gevonden op de buitendiameters van de buizen.
De 9-5/8''-behuizing werd ook gesneden en getrokken en vergelijkbare effecten werden waargenomen;met slechts aan één zijde corrosie in het bovenste gedeelte van de put.Het geïnduceerde lek werd veroorzaakt door het barsten van het verzwakte deel van de behuizing.
Het materiaal van de chemische injectieleiding was legering 825.
Chemische kwalificatie
Chemische eigenschappen en corrosietesten zijn belangrijke aandachtspunten bij de kwalificatie van aanslagremmers en de eigenlijke aanslagremmer is al meerdere jaren gekwalificeerd en gebruikt in boven- en onderzeese toepassingen.De reden voor het toepassen van de eigenlijke chemische stof in het boorgat was verbeterde milieu-eigenschappen door de bestaande chemische stof in het boorgat te vervangen. De aanslagremmer was echter alleen gebruikt bij omgevingstemperaturen aan de bovenkant en op de zeebodem (4-20 ℃).Wanneer het in de put werd geïnjecteerd, kon de temperatuur van de chemische stof oplopen tot 90 ℃, maar er waren geen verdere tests uitgevoerd bij deze temperatuur.
De eerste corrosiviteitstests waren uitgevoerd door de leverancier van chemicaliën en de resultaten toonden 2-4 mm/jaar voor koolstofstaal bij hoge temperaturen.Tijdens deze fase was er minimale betrokkenheid van de materiaaltechnische competentie van de operator.Later werden door de operator nieuwe tests uitgevoerd die aantoonden dat de aanslagremmer zeer corrosief was voor de materialen in de productiebuizen en de productiebehuizing, met corrosiesnelheden van meer dan 70 mm/jaar.Het materiaal van de chemische injectieleiding Alloy 825 was voorafgaand aan de injectie niet getest op de aanslagremmer.De puttemperatuur kan oplopen tot 90 ℃ en onder deze omstandigheden zouden adequate tests moeten zijn uitgevoerd.
Het onderzoek bracht ook aan het licht dat de aanslagremmer als geconcentreerde oplossing een pH van <3,0 had gerapporteerd.De pH was echter niet gemeten.Later toonde de gemeten pH een zeer lage waarde van pH 0-1.Dit illustreert de behoefte aan metingen en materiaaloverwegingen naast gegeven pH-waarden.
Interpretatie van de resultaten
De injectieleiding (fig. 3) is geconstrueerd om een hydrostatische druk van de kalkremmer te geven die hoger is dan de druk op het injectiepunt.De remmer wordt geïnjecteerd bij een hogere druk dan in de boorput.Dit resulteert in een U-buiseffect bij het insluiten van de put.De klep zal altijd openen bij een hogere druk in de injectieleiding dan in de put.Er kan daardoor vacuüm of verdamping in de injectieleiding ontstaan.De corrosiesnelheid en het risico op putcorrosie is het grootst in de overgangszone gas/vloeistof door verdamping van het oplosmiddel.Laboratoriumexperimenten uitgevoerd op coupons bevestigden deze theorie.In de putten waar lekkage werd ervaren, bevonden alle gaten in de injectieleidingen zich in het bovenste deel van de chemicaliëninjectieleiding.
Fig. 4 toont fotografie van de DHC I-lijn met aanzienlijke putcorrosie.De corrosie op de buitenste productieslang duidde op een lokale blootstelling van de aanslagremmer vanaf het punt van putjeslekkage.De lekkage werd veroorzaakt door putcorrosie door zeer corrosieve chemicaliën en lekkage via de injectieleiding voor chemicaliën in de productiebehuizing.De aanslagremmer werd vanuit de capillaire lijn met putjes op de behuizing en de slangen gespoten en er ontstonden lekken.Er was geen rekening gehouden met eventuele secundaire gevolgen van lekkages in de injectieleiding.Er werd geconcludeerd dat de corrosie van de behuizing en de slangen het gevolg was van geconcentreerde aanslagremmers die vanuit de putjes in de capillaire leiding op de behuizing en de slangen werden aangebracht, Fig.5.
In dit geval was er een gebrek aan betrokkenheid van materiaalexpertise.Corrosiviteit van de chemische stof op de DHCI-lijn was niet getest en de secundaire effecten als gevolg van lekkage waren niet geëvalueerd;zoals of de omliggende materialen blootstelling aan chemicaliën zouden kunnen verdragen.
Casusgeschiedenis van de koning met chemische wapens
Volgorde van de gebeurtenissen
De strategie voor het voorkomen van aanslag voor een HP HT-veld was continue injectie van aanslagremmer stroomopwaarts van de veiligheidsklep in het boorgat.In de put werd een ernstig potentieel voor calciumcarbonaatafzetting vastgesteld.Een van de uitdagingen was de hoge temperatuur en de hoge gas- en condensaatproductie in combinatie met de lage waterproductie.De zorg door het injecteren van een aanslagremmer was dat het oplosmiddel zou worden verwijderd door de hoge gasproductiesnelheid en dat de chemische stof zou vrijkomen op het injectiepunt stroomopwaarts van de veiligheidsklep in de put, Fig.1.
Tijdens de kwalificatie van de kalkremmer lag de focus op de efficiëntie van het product bij HP HT-omstandigheden, inclusief het gedrag in het processysteem aan de bovenzijde (lage temperatuur).Neerslag van de aanslagremmer zelf in de productieslangen als gevolg van de hoge gassnelheid was de grootste zorg.Laboratoriumtesten toonden aan dat een kalkremmer zou kunnen neerslaan en zich aan de buiswand zou kunnen hechten.De werking van de veiligheidsklep kan daarom beter zijn dan het risico.
De ervaring leerde dat na een paar weken gebruik de chemicaliënleiding lekte.Het was mogelijk om de boorputdruk te bewaken aan de oppervlaktemeter die in de capillaire leiding was geïnstalleerd.De lijn werd geïsoleerd om putintegriteit te verkrijgen.
De chemische injectieleiding werd uit de put getrokken, geopend en geïnspecteerd om het probleem te diagnosticeren en mogelijke redenen voor het falen te vinden.Zoals te zien is in figuur 6, werd een aanzienlijke hoeveelheid neerslag gevonden en chemische analyse toonde aan dat een deel hiervan de aanslagremmer was.Het neerslag bevond zich bij de afdichting en de schotel en de klep kon niet worden bediend.
De storing van de klep werd veroorzaakt door vuil in het klepsysteem, waardoor de terugslagkleppen niet aan de metaal-op-metaal zitting konden vreten.Het puin werd onderzocht en de belangrijkste deeltjes bleken metaalkrullen te zijn, waarschijnlijk geproduceerd tijdens het installatieproces van de capillaire lijn.Bovendien werd wat wit vuil gevonden op beide keerkleppen, vooral aan de achterkant van de kleppen.Dit is de lagedrukzijde, dwz de zijde die altijd in contact zou zijn met de boorvloeistoffen.Aanvankelijk werd aangenomen dat dit puin uit de productieputboring was, aangezien de kleppen open waren geklemd en waren blootgesteld aan boorputvloeistoffen.Maar bij onderzoek bleek het puin polymeren te zijn met een vergelijkbare chemie als de chemische stof die als aanslagremmer werd gebruikt.Dit trok onze interesse en Statoil wilde de redenen onderzoeken achter dit polymeerafval in de capillaire leiding.
Chemische kwalificatie
In een HP HT-veld zijn er veel uitdagingen met betrekking tot de selectie van geschikte chemicaliën om de verschillende productieproblemen te verminderen.Bij de kwalificatie van de aanslagremmer voor continue injectie in het boorgat zijn de volgende tests uitgevoerd:
● Productstabiliteit
● Thermische veroudering
● Dynamische prestatietests
● Compatibiliteit met formatiewater en hydraatremmer (MEG)
● Statische en dynamische pistoolkoningtest
● Re-oplossing informatie water, verse chemicaliën en MEG
De chemische stof wordt geïnjecteerd met een vooraf bepaalde dosering,maar de waterproductie zal niet noodzakelijkerwijs constant zijn,dwz waterslugging.Tussen de waterslakken door,wanneer de chemische stof de boorput binnenkomt,het zal worden opgewacht door een hete,snelstromende stroom koolwaterstofgas.Dit is vergelijkbaar met het injecteren van een kalkremmer in een gaslifttoepassing (Fleming etal.2003). Samen met
de hoge gastemperatuur,het risico van het strippen van oplosmiddel is extreem hoog en gun king kan verstopping van de injectieklep veroorzaken.Dit is zelfs een risico voor chemicaliën die zijn geformuleerd met oplosmiddelen met een hoog kookpunt/lage dampdruk en andere dampdrukverlagende middelen (VPD's). In het geval van een gedeeltelijke verstopping,stroom van formatiewater,MEG en/of verse chemicaliën moeten in staat zijn om de gedehydrateerde of uitgesmeerde chemicaliën te verwijderen of opnieuw op te lossen.
In dit geval werd een nieuwe laboratoriumtestopstelling ontworpen om stromingsomstandigheden nabij de injectiepoorten bij een HP/HTg als productiesysteem na te bootsen.De resultaten van de dynamische Gun King-testen tonen aan dat er onder de voorgestelde toepassingsomstandigheden een aanzienlijk verlies aan oplosmiddel werd geregistreerd.Dit zou kunnen leiden tot snelle gun king en uiteindelijk blokkering van de stroomlijnen.Het werk toonde daarom aan dat er een relatief groot risico bestond voor continue chemicaliëninjectie in deze putten voorafgaand aan de waterproductie en leidde tot de beslissing om de normale opstartprocedures voor dit veld aan te passen, waarbij de injectie van chemicaliën werd uitgesteld totdat er waterdoorbraak werd gedetecteerd.
De kwalificatie van ketelsteenremmer voor continue injectie in het boorgat was sterk gericht op het strippen van oplosmiddel en gun king van de ketelsteenremmer op het injectiepunt en in de stroomleiding, maar het potentieel voor gun king in de injectieklep zelf werd niet geëvalueerd.De injectieklep faalde waarschijnlijk vanwege aanzienlijk verlies van oplosmiddel en snelle pistoolkoning,Fig.6.De resultaten laten zien dat het belangrijk is om een holistisch beeld van het systeem te hebben;focus niet alleen op de productie-uitdagingen,maar ook uitdagingen met betrekking tot de injectie van de chemische stof,dwz injectieklep.
Ervaring uit andere vakgebieden
Een van de eerste rapporten over problemen met chemicaliëninjectielijnen over lange afstanden was afkomstig van de Gull fak sandVigdis-satellietvelden (Osa etal.2001). De onderzeese injectielijnen waren geblokkeerd voor hydraatvorming in de lijn als gevolg van het binnendringen van gas uit de geproduceerde vloeistoffen. in de leiding via de injectieklep.Er werden nieuwe richtlijnen ontwikkeld voor de ontwikkeling van onderzeese productiechemicaliën.De vereisten omvatten het verwijderen van deeltjes (filtratie) en toevoeging van hydraatremmer (bijv. glycol) aan alle op water gebaseerde ketelsteenremmers die in de onderzeese sjablonen moeten worden geïnjecteerd.Chemische stabiliteit,viscositeit en compatibiliteit (vloeistof en materialen) werden ook overwogen.Deze vereisten zijn verder in het Statoil-systeem opgenomen en omvatten chemische injectie in het boorgat.
Tijdens de ontwikkelingsfase van de Oseberg S of het veld werd besloten dat alle putten zouden worden aangevuld met DHC I-systemen (Fleming etal.2006). Het doel was om CaCO te voorkomen;schilfering in de bovenste slang door SI-injectie.Een van de grootste uitdagingen met betrekking tot de injectieleidingen voor chemicaliën was het tot stand brengen van communicatie tussen het oppervlak en de uitlaat onder in het boorgat.De interne diameter van de injectieleiding voor chemicaliën versmalde van 7 mm tot 0,7 mm (ID) rond de ringvormige veiligheidsklep vanwege ruimtebeperkingen en het vermogen van de vloeistof om door dit gedeelte te worden getransporteerd, had invloed op het slagingspercentage.Verschillende platformputten hadden chemicaliëninjectieleidingen die verstopt waren,maar de reden werd niet begrepen.Treinen van verschillende vloeistoffen (glycol,ruw,condensaat,xyleen,schaal remmer,water enz.) zijn in het laboratorium getest op viscositeit en compatibiliteit en voorwaarts en in omgekeerde richting gepompt om de leidingen te openen;Echter,de beoogde aanslagremmer kon niet helemaal naar de chemische injectieklep worden gepompt.Verder,complicaties werden waargenomen met precipitatie van de fosfonaataanslagremmer samen met resterende CaClz-aanvullingspekel in één put en gun king of the scale-remmer in een put met een hoge gasolieverhouding en een lage waterafsnijding (Fleming etal.2006)
Les geleerd
Ontwikkeling testmethode
De belangrijkste lessen die uit het falen van DHC I-systemen zijn getrokken, hebben betrekking op de technische efficiëntie van de aanslagremmer en niet op de functionaliteit en chemische injectie.Topside-injectie en subsea-injectie hebben overuren goed gefunctioneerd;Echter,de toepassing is uitgebreid tot chemische injectie in het boorgat zonder een overeenkomstige update van de chemische kwalificatiemethoden.Statoil's ervaring met de twee gepresenteerde veldcases is dat de geldende documentatie of richtlijnen voor chemische kwalificatie moeten worden bijgewerkt om dit type chemische toepassing op te nemen.De belangrijkste twee uitdagingen zijn geïdentificeerd als i) vacuüm in de chemische injectielijn en ii) mogelijke neerslag van de chemische stof.
Verdamping van de chemische stof kan optreden op de productieslang (zoals te zien in de Gun King-behuizing) en in de injectieslang (in de vacuümbehuizing is een tijdelijke interface geïdentificeerd). Er bestaat een risico dat deze precipitaten met de stroom worden verplaatst en in de injectieklep en verder in de put.De injectieklep is vaak ontworpen met een filter stroomopwaarts van het injectiepunt,dit is een uitdaging,aangezien bij neerslag dit filter verstopt kan raken waardoor de klep defect raakt.
De observaties en voorlopige conclusies van de geleerde lessen resulteerden in een uitgebreid laboratoriumonderzoek naar de verschijnselen.Het algemene doel was om nieuwe kwalificatiemethoden te ontwikkelen om soortgelijke problemen in de toekomst te voorkomen.In deze studie zijn verschillende tests uitgevoerd en zijn verschillende laboratoriummethoden ontworpen (ontwikkeld om) om chemicaliën te onderzoeken met betrekking tot de geïdentificeerde uitdagingen.
● Filterverstoppingen en productstabiliteit in gesloten systemen.
● Het effect van gedeeltelijk oplosmiddelverlies op de corrosiviteit van de chemicaliën.
● Het effect van gedeeltelijk verlies van oplosmiddel in een capillair op de vorming van vaste stoffen of stroperige pluggen.
Tijdens de tests van de laboratoriummethoden zijn verschillende potentiële problemen geïdentificeerd
● Herhaalde filterblokkades en slechte stabiliteit.
● Vorming van vaste stoffen na gedeeltelijke verdamping uit een capillair
● PH verandert als gevolg van verlies van oplosmiddel.
De aard van de uitgevoerde tests heeft ook aanvullende informatie en kennis opgeleverd met betrekking tot veranderingen in de fysische eigenschappen van chemicaliën in capillairen wanneer ze aan bepaalde omstandigheden worden onderworpen,en hoe dit verschilt van bulkoplossingen die aan vergelijkbare omstandigheden worden onderworpen.Het testwerk heeft ook aanzienlijke verschillen tussen de bulkvloeistof aan het licht gebracht,dampfasen en achtergebleven vloeistoffen, wat kan leiden tot ofwel een grotere kans op neerslag en/of een verhoogde corrosiviteit.
De testprocedure voor corrosiviteit van de kalkremmers is ontwikkeld en opgenomen in de geldende documentatie.Voor elke toepassing moesten uitgebreide corrosiviteitstests worden uitgevoerd voordat injectie van kalkremmer kon worden geïmplementeerd.Gun king-testen van de chemische stof in de injectieleiding zijn ook uitgevoerd.
Voordat u begint met de kwalificatie van een chemische stof, is het belangrijk om een werkgebied te creëren waarin de uitdagingen en het doel van de chemische stof worden beschreven.In de beginfase is het belangrijk om de belangrijkste uitdagingen te identificeren om de soorten chemicaliën te kunnen selecteren die het probleem zullen oplossen.Een overzicht van de belangrijkste acceptatiecriteria is te vinden in tabel 2.
Kwalificatie van chemicaliën
Kwalificatie van chemicaliën bestaat uit zowel testen als theoretische evaluaties voor elke toepassing.Technische specificaties en testcriteria moeten worden gedefinieerd en vastgesteld,bijvoorbeeld binnen HSE,materiële compatibiliteit,productstabiliteit en productkwaliteit (deeltjes).Verder,het vriespunt,viscositeit en compatibiliteit met andere chemicaliën,hydraat remmer,formatiewater en de geproduceerde vloeistof moeten worden bepaald.Tabel 2 bevat een vereenvoudigde lijst van testmethoden die kunnen worden gebruikt voor de kwalificatie van chemische stoffen.
Continue focus op en bewaking van de technische efficiëntie,doseringen en VGM-feiten zijn belangrijk.De vereisten van een product kunnen veranderen tijdens de levensduur van een veld of procesinstallatie;variëren met productiesnelheden en vloeistofsamenstelling.Vervolgactiviteit met evaluatie van de prestaties,optimalisatie en/of testen van nieuwe chemicaliën moet regelmatig worden gedaan om het optimale behandelingsprogramma te garanderen.
Afhankelijk van de oliekwaliteit,waterproductie en technische uitdagingen bij de offshore productiefabriek,het gebruik van productiechemicaliën kan nodig zijn om exportkwaliteit te bereiken,wettelijke vereisten,en om de offshore installatie op een veilige manier te bedienen.Alle velden hebben verschillende uitdagingen en de benodigde productiechemicaliën variëren van veld tot veld en overuren.
Het is belangrijk om in een kwalificatieprogramma aandacht te besteden aan technische efficiëntie van productiechemicaliën,maar het is ook erg belangrijk om je te concentreren op de eigenschappen van de chemische stof,zoals stabiliteit,productkwaliteit en compatibiliteit.Compatibiliteit in deze instelling betekent compatibiliteit met de vloeistoffen,materialen en andere productiechemicaliën.Dit kan een uitdaging zijn.Het is niet wenselijk om een chemische stof te gebruiken om een probleem op te lossen om later te ontdekken dat de chemische stof bijdraagt aan of nieuwe uitdagingen creëert.Misschien zijn de eigenschappen van de chemische stof en niet de technische uitdaging de grootste uitdaging.
Speciale vereisten
Voor het onderzeese systeem en voor continue injectie in het boorgat moeten speciale eisen worden gesteld aan de filtratie van geleverde producten.Er moeten zeven en filters in het injectiesysteem voor chemicaliën worden aangebracht op basis van de specificatie op de stroomafwaartse apparatuur van het injectiesysteem aan de bovenzijde,pompen en injectieventielen,naar de injectiekleppen in het boorgat.Waar continue injectie van chemicaliën in het boorgat wordt toegepast, moet de specificatie in het chemicaliëninjectiesysteem gebaseerd zijn op de specificatie met de hoogste kriticiteit.Dit is misschien het filter bij de injectieklep beneden in het boorgat.
Injectie uitdagingen
Het injectiesysteem kan een afstand van 3-50 km van de navelstreng onderzeese stroomlijn en 1-3 km naar beneden in de put impliceren.Fysische eigenschappen zoals viscositeit en het vermogen om de chemicaliën te verpompen zijn belangrijk.Als de viscositeit bij zeebodemtemperatuur te hoog is, kan het een uitdaging zijn om de chemische stof door de chemische injectieleiding in de onderzeese navelstreng naar het onderzeese injectiepunt of in de put te pompen.De viscositeit moet overeenkomen met de systeemspecificatie bij de verwachte opslag- of bedrijfstemperatuur.Dit moet in elk geval worden beoordeeld,en zal systeemafhankelijk zijn.Aangezien de injectiesnelheid van tafelchemicaliën een succesfactor is bij het injecteren van chemicaliën.Om het risico van verstopping van de injectieleiding voor chemicaliën te minimaliseren,de chemicaliën in dit systeem moeten hydraatgeremd zijn (indien mogelijk voor hydraten).Compatibiliteit met in het systeem aanwezige vloeistoffen (conserveringsvloeistof) en de hydraatremmer moet worden uitgevoerd.Stabiliteitstests van de chemische stof bij werkelijke temperaturen (laagst mogelijke omgevingstemperatuur,omgevingstemperatuur,onderzeese temperatuur,injectietemperatuur) moeten worden gepasseerd.
Er moet ook een programma worden overwogen om de injectieleidingen voor chemicaliën met een bepaalde frequentie te wassen.Het kan preventief werken om de injectieleiding voor chemicaliën regelmatig door te spoelen met oplosmiddel,glycol of chemisch reinigingsmiddel om mogelijke afzettingen te verwijderen voordat deze zich ophopen en verstopping van de leiding kunnen veroorzaken.De gekozen chemische oplossing van spoelvloeistof moet zijncompatibel met de chemische stof in de injectieleiding.
In sommige gevallen wordt de injectielijn voor chemicaliën gebruikt voor verschillende chemische toepassingen op basis van verschillende uitdagingen gedurende een veldleven en vloeistofomstandigheden.In de initiële productiefase voordat het water doorbreekt, kunnen de belangrijkste uitdagingen verschillen van die aan het eind van het leven, vaak gerelateerd aan verhoogde waterproductie.Het overstappen van een niet-waterige remmer op basis van oplosmiddelen, zoals een remmer van asfalteen, naar een chemische stof op waterbasis, zoals een kalkremmer, kan compatibiliteitsproblemen opleveren.Het is daarom belangrijk om te focussen op compatibiliteit en kwalificatie en het gebruik van afstandhouders wanneer het de bedoeling is om chemicaliën in de chemicaliëninjectielijn te vervangen.
Materialen
Wat betreft materiaalcompatibiliteit,alle chemicaliën moeten compatibel zijn met afdichtingen,elastomeren,pakkingen en constructiematerialen die worden gebruikt in het chemische injectiesysteem en de productie-installatie.Er moet een testprocedure voor de corrosiviteit van chemicaliën (bijv. zure aanslagremmer) voor continue injectie in het boorgat worden ontwikkeld.Voor elke toepassing moeten uitgebreide corrosiviteitstests worden uitgevoerd voordat injectie van chemicaliën kan worden geïmplementeerd.
Discussie
De voor- en nadelen van continue chemische injectie in het boorgat moeten worden geëvalueerd.Continue injectie van ketelsteenremmer om de DHS te beschermen. Vor de productieslang is een elegante methode om de put tegen aanslag te beschermen.Zoals vermeld in dit artikel zijn er verschillende uitdagingen met continue chemische injectie in het boorgat,om het risico echter te verminderen, is het belangrijk om de fenomenen die verband houden met de oplossing te begrijpen.
Een manier om het risico te verminderen, is door te focussen op de ontwikkeling van testmethoden.Vergeleken met chemicaliëninjectie aan de bovenzijde of onder water zijn er verschillende en zwaardere omstandigheden beneden in de put.De kwalificatieprocedure voor chemicaliën voor continue injectie van chemicaliën in het boorgat moet rekening houden met deze veranderingen in omstandigheden.De kwalificatie van de chemicaliën moet worden gemaakt op basis van het materiaal waarmee de chemicaliën in contact kunnen komen.De vereisten voor compatibiliteitskwalificatie en testen onder omstandigheden die de verschillende levenscyclusomstandigheden van de put zo goed mogelijk nabootsen waaronder deze systemen zullen werken, moeten worden bijgewerkt en geïmplementeerd.De ontwikkeling van de testmethode moet verder ontwikkeld worden naar meer realistische en representatieve testen.
In aanvulling,de interactie tussen de chemicaliën en de apparatuur is essentieel voor succes.Bij de ontwikkeling van de chemische injectiekleppen moet rekening worden gehouden met de chemische eigenschappen en de locatie van de injectieklep in de put.Er moet worden overwogen om echte injectiekleppen op te nemen als onderdeel van de testapparatuur en om prestatietests uit te voeren van de aanslagremmer en het ontwerp van de klep als onderdeel van het kwalificatieprogramma.Schaalremmers kwalificeren,de belangrijkste focus lag eerder op de procesuitdagingen en schaalremming,maar goede schaalremming hangt af van stabiele en continue injectie.Zonder stabiele en continue injectie neemt de kans op schaalvergroting toe.Als het kalkremmer-injectieventiel verstopt is en er geen kalkremmer-injectie in de vloeistofstroom is,de put en de veiligheidskleppen zijn niet beschermd tegen kalkaanslag en daarom kan een veilige productie in gevaar komen.De kwalificatieprocedure moet zorgen voor de uitdagingen die verband houden met de injectie van de kalkremmer, naast de procesuitdagingen en de efficiëntie van de gekwalificeerde kalkremmer.
Bij de nieuwe aanpak zijn meerdere disciplines betrokken en de samenwerking tussen de disciplines en de respectievelijke verantwoordelijkheden moeten worden verduidelijkt.In deze toepassing het bovenzijde processysteem,onderzeese sjablonen en ontwerp en voltooiing van putten zijn hierbij betrokken.Multidisciplinaire netwerken gericht op het ontwikkelen van robuuste oplossingen voor chemische injectiesystemen zijn belangrijk en misschien wel de weg naar succes.De communicatie tussen de verschillende disciplines is cruciaal;vooral nauwe communicatie tussen de chemici die de controle hebben over de toegepaste chemicaliën en de putingenieurs die de controle hebben over de apparatuur die in de put wordt gebruikt, is belangrijk.Om de complexiteit van het hele proces te begrijpen, is het essentieel om de uitdagingen van de verschillende disciplines te begrijpen en van elkaar te leren.
Conclusie
● Continue injectie van kalkremmer om de DHS te beschermen. Vor de productieslang is een elegante methode om de put te beschermen tegen kalkaanslag
● Om de geïdentificeerde uitdagingen op te lossen,volgende aanbevelingen zijn:
● Er moet een speciale DHCI-kwalificatieprocedure worden uitgevoerd.
● Kwalificatiemethode voor chemicaliëninjectieventielen
● Test- en kwalificatiemethoden voor chemische functionaliteit
● Methodeontwikkeling
● Relevante materiaaltesten
● Het multidisciplinaire samenspel waarbij communicatie tussen de verschillende betrokken disciplines cruciaal is voor succes.
Dankbetuigingen
De auteur wil Statoil AS A bedanken voor toestemming om dit werk te publiceren en Baker Hughes en Schlumberger voor het toestaan van het gebruik van de afbeelding in Fig.2.
Nomenclatuur
(Ba/Sr)SO4=barium/strontiumsulfaat
CaCO3=calciumcarbonaat
DHCI = chemische injectie in het boorgat
DHSV=downhole veiligheidsklep
bijv.=bijvoorbeeld
GOR=gasolieverhouding
HSE = gezondheidsveiligheidsomgeving
HPHT=hoge druk hoge temperatuur
ID=binnendiameter
oftewel = dat is
km=kilometer
mm=millimeter
MEG=mono-ethyleenglycol
mMD=meter gemeten diepte
OD=buitendiameter
SI = schaalremmer
mTV D=meter totale verticale diepte
U-buis=U-vormige buis
VPD = dampdrukverlagend middel
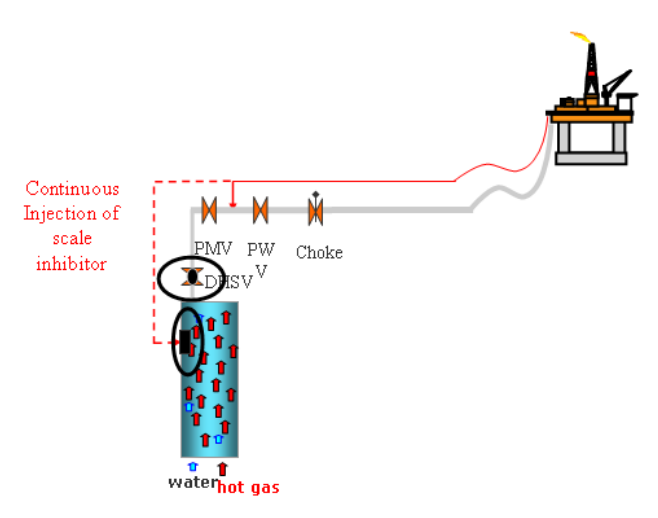
Figuur 1. Overzicht van de onderzeese en ondergrondse chemische injectiesystemen in een atypisch veld.Schets van chemische injectie stroomopwaarts DHSV en de gerelateerde verwachte uitdagingen.DHS V=downhole veiligheidsklep, PWV=proces vleugelklep en PM V=proces hoofdklep.
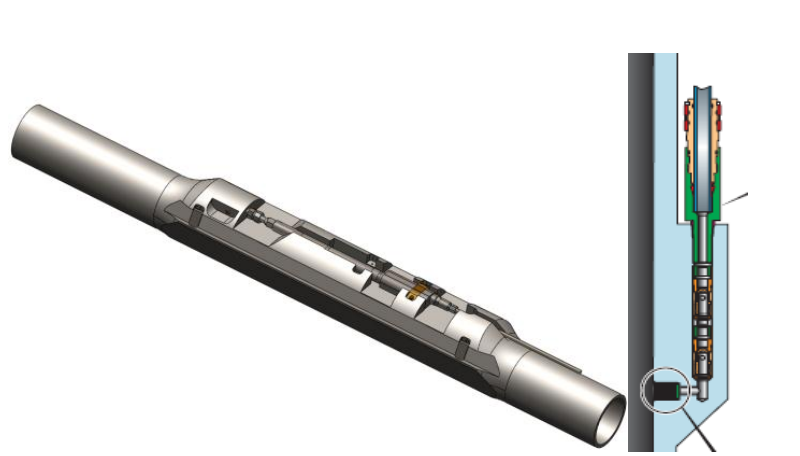
Figuur 2. Schets van een atypisch chemisch injectiesysteem in het boorgat met de doorn en klep.Het systeem wordt aangesloten op het verdeelstuk aan de oppervlakte, er doorheen gevoerd en verbonden met de slanghanger aan de ringvormige zijde van de slang.De doorn voor chemische injectie wordt traditioneel diep in de put geplaatst met de bedoeling om chemische bescherming te bieden.
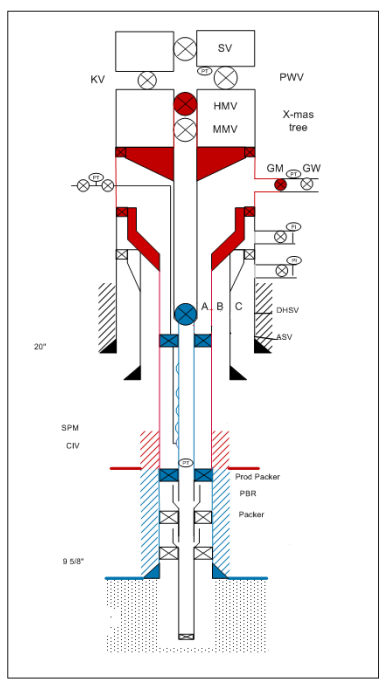
Figuur 3. Typisch schema van een putbarrière,waarbij de blauwe kleur de omhulling van de primaire putbarrière vertegenwoordigt;in dit geval de productieslang.De rode kleur vertegenwoordigt de secundaire barrière-envelop;het omhulsel.Aan de linkerkant is de chemische injectie aangegeven, zwarte lijn met injectiepunt naar de productieslang in het rood gemarkeerde gebied (secundaire barrière).
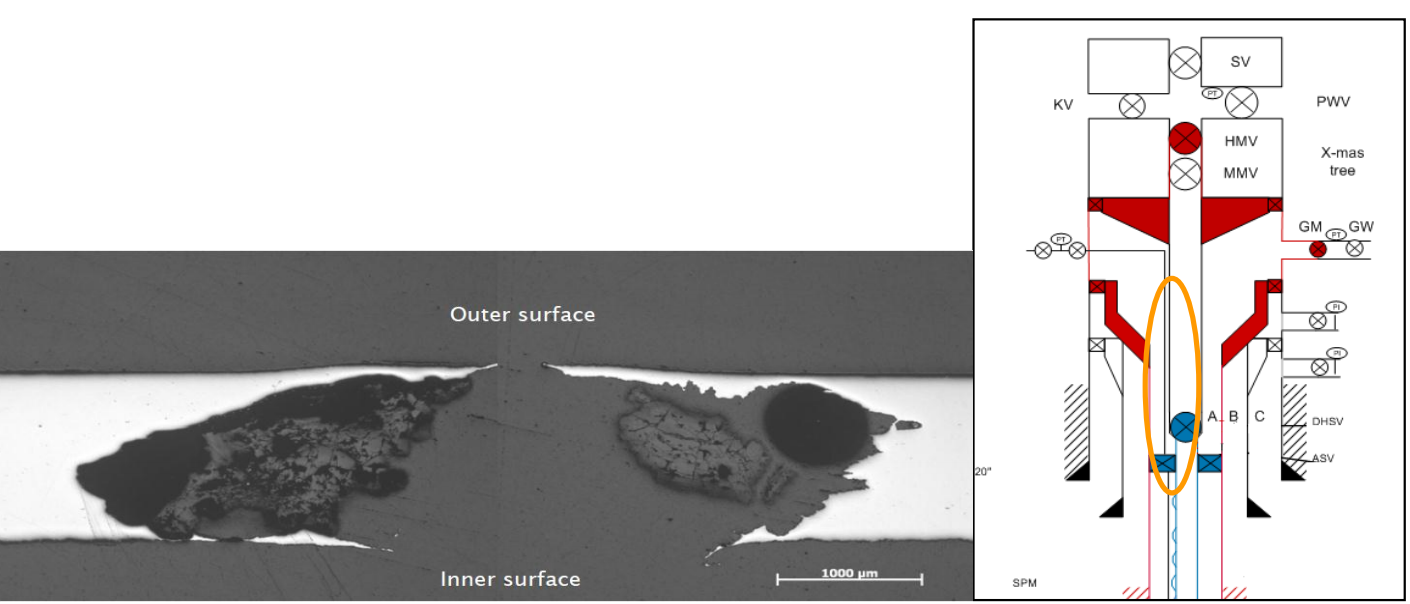
Afbeelding 4. Putje gevonden in het bovenste gedeelte van de 3/8” injectieleiding.Het gebied wordt getoond in de schets van een atypisch putbarrièreschema, gemarkeerd met een oranje ellips.
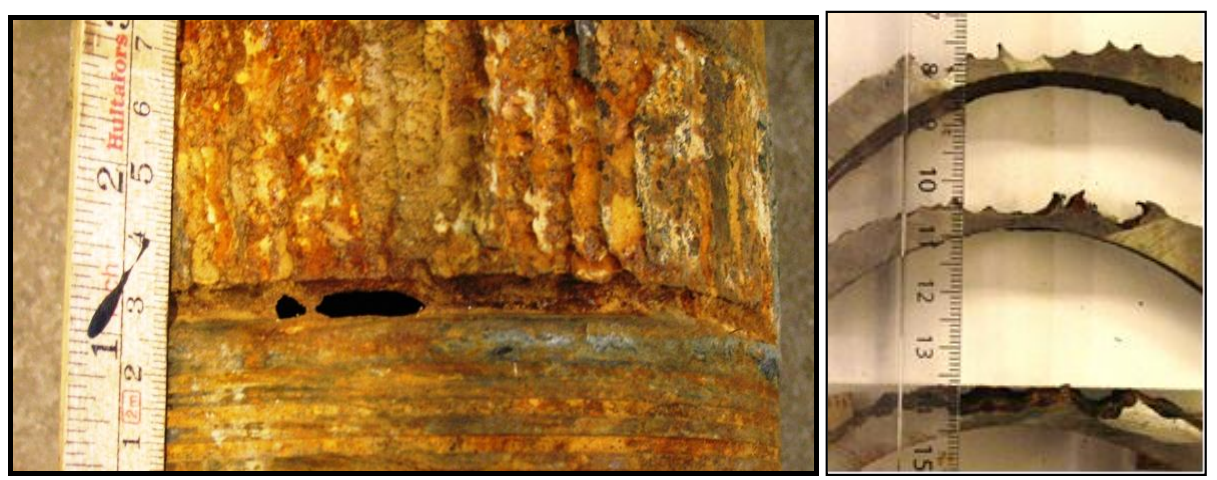
Afbeelding 5. Ernstige aantasting door corrosie van de 7” 3% Chrome-slang.De afbeelding toont de aantasting door corrosie na het sproeien van een kalkremmer uit de chemische injectieleiding met putjes op de productieslang.
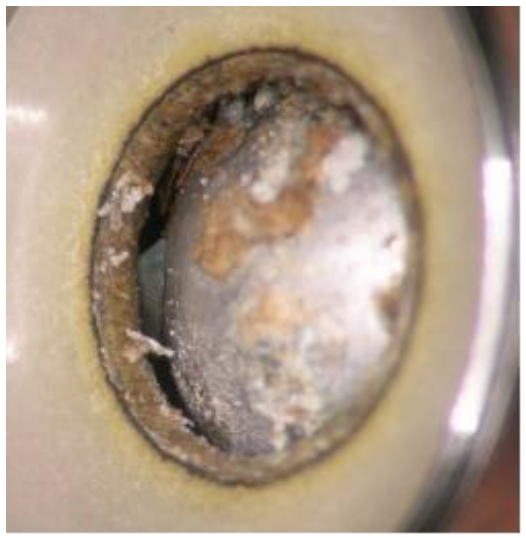
Afbeelding 6. Vuil gevonden in de injectieklep voor chemicaliën.Het puin was in dit geval metaalspaanders waarschijnlijk van het installatieproces naast wat witachtig puin.Onderzoek van het witte puin bleek polymeren te zijn met een vergelijkbare chemie als de geïnjecteerde chemische stof
Posttijd: 27 april 2022